A hospital isn’t “completed” just because construction has ended. To ensure a hospital’s health, marrying design with facility operations comes into play. One way to think about healthcare facilities services, which includes the departments that make up Materials Management, is to think of the human circulation system. A good, strong heart ensures an unobstructed flow of materials to keep everything moving efficiently and effectively through the system. Materials management services are in many ways the heart and lifeblood of the facility.
Components of Facility Layout and Materials Management
There are many moving parts in healthcare facilities, all with unique design challenges. Some of the more important ones are:
- Loading Docks. The coordination of supply trucks and waste stream movement cane be challenging and requires the dock area to be sized correctly to accommodate both clean and soiled waste streams, as well as located conveniently. Regulatory and Licensing agencies stringently enforce separation of clean supply and waste to minimize overlap.
- Materials Management. Storage of supplies and equipment often are not integrated with physician needs, resulting in too many of some supplies and too few of others. Connecting supply vendors with the hospitals electronic records system is a way to track real-time information on how many supplies are currently on hand, where they are located, and what’s in stock. Hospitals are required to have 20 square-feet per bed minimum storage on hand. Ensuring that the overall supply space is used efficiently can reduce overhead costs.
- Environmental Services. These are services required to maintain cleanliness and infection control. Efficient design is required to ensure that flows of both clean and soiled materials are separated to minimize contamination.
- Mailroom and Courier Services. Even though hospital facilities are moving towards more digital services, there are still plenty of transactions that happen through physical mailings. Having a system that allows incoming and outgoing mail to happen easily is often overlooked, but just as important for day-to-day function.
- Dietary Services. There are many people that need to be fed within a hospital environment. Dietary services have the challenge of having patient meals that are delivered hot from a remote location within the facility which is a difficult proposition as patients are not always in their rooms when meals are delivered.
- Waste Management. Managing hospital waste is an expensive proposition for owners. Hospital trash needs to be sorted for recycling, biological waste needs to be held separately and stored before sending to a landfill. Food waste – depending on the municipality needs to be managed carefully for landfill or composting. Chemical, Radioactive, Pathological, Sharps and Pharmaceutical waste are also part of the waste stream that requires careful management.
Facilities departments are typically located in “back of house” locations within a hospital. They are located together, as their functions are similar, and are almost always located on either a basement floor level or ground floor and have access to truck deliveries, corridors and service elevators for multi-story hospitals.
Understanding Material Management for Facility Layout
The various material management components support clinical and administrative work in the hospital. As such, a deep understanding of the sizing, operations, and flows associated with each department is required when designing a hospital. The general goals for the broad category of materials management are to acquire the optimum pricing for supplies, optimize inventory turnover, maintain cost control, effectively distribute thru the facility, and to eliminate losses and theft.
Material management is so important to hospital executives because there is a huge amount of financial resources tied up in it. It’s estimated that 30-35 percent of recurring expenditures are materials, and the cost of labor for these services are considered overhead costs, which are non-reimbursable by insurance providers. Approximately 25 percent of the costs are carried by the facility, tied up in storage, manpower, obsolete equipment, and theft/breakage, which is over and above purchase costs.
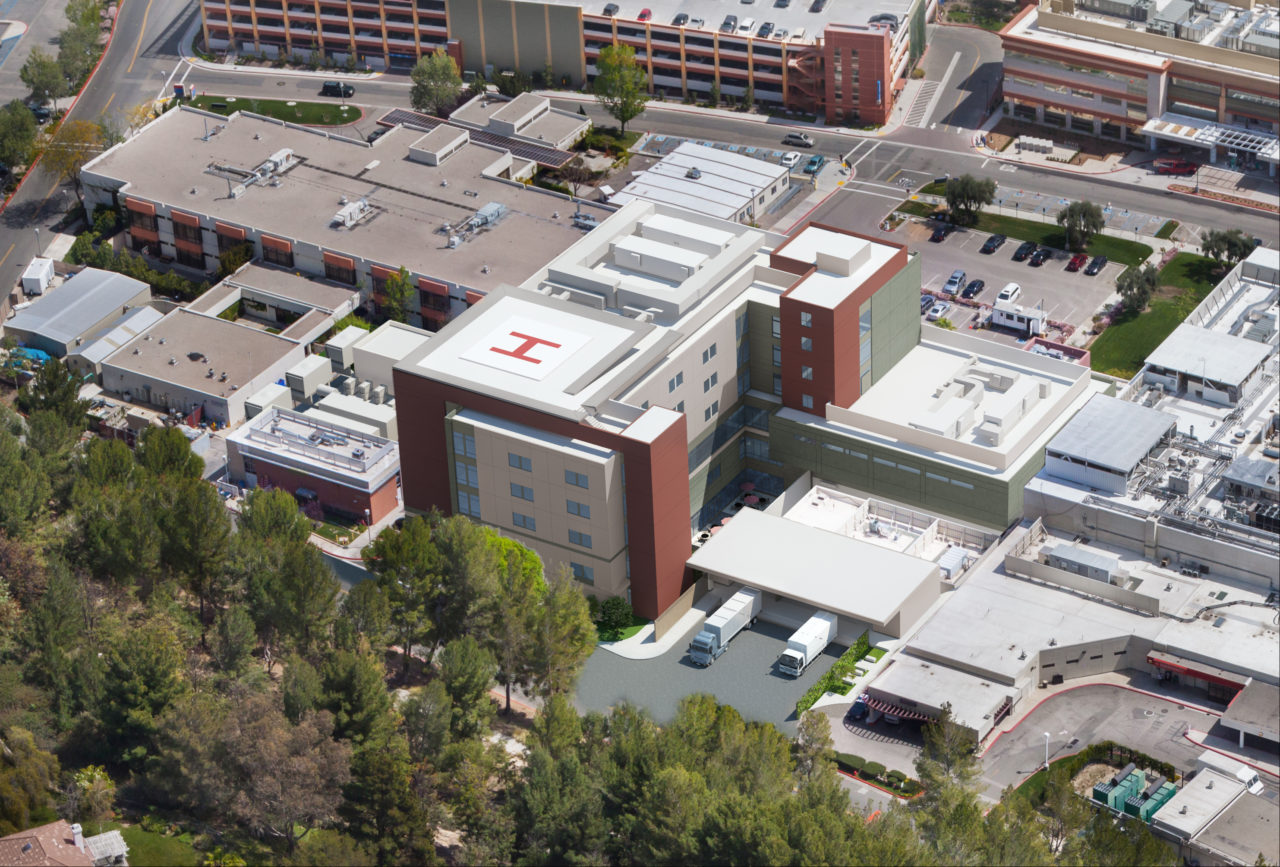
The loading dock at Henry Mayo Newhall Hospital in Valencia, California.
How to Improve Operations Tied to Planning
Material Management and Purchasing can have improved supply chain operations through collaborative planning. Some effective techniques for this are:
- Providing RFID tagging on equipment and supplies so they can be located and tracked.
- Outsourcing distribution and delivery to hospital vendors, which allows the facility to share the burden of resource allocation, can provide a “just-in-time” supply stream to minimize storage needs.
- Connect the hospital-based electronic data systems such as Epic or Cerna, to vendors to determine what they are going to need and when.
- Look at operations and flow less from a “clinical” need, and more from an “operational flow” perspective. Opportunities to re-engineer a space and process can provide a better process and reduced costs.
Another huge component in operations is the dietary service needs. Hospitals face significant challenges in delivering high quality and hot food for patients for many reasons. Dietary restrictions complicate matters because facilities need to customize food orders, and patients are sometimes not in rooms when food is delivered. Most facilities employ what’s called cook to order food and go through a process of plating food on an assembly line of sorts to send to the room. The challenge to this operational model is that from the moment food is plated to the time it’s served in the room, it is cooling off.
An improved approach to this problem would be to evaluate operational improvements such as “cook-chill” production to ensure patient meals are high quality and hot when served. In this process, food is cooked in bulk, rapidly chilled and stored in bags for up to a month in advance. The process of plating the food is to start cold and send it to a pantry on the nursing unit, where it is reheated and served when the patient is in the room and ready. Looking into the future towards more tech-savvy solutions, distributing food in advance by automated guided vehicles is another way to improve efficiencies.
Managing Waste Effectively
The most challenging and costly part of the Materials Management system is the segregation, safe handling, and disposal of hospital waste – particularly that of Infectious medical waste. In addition to the myriad of federal, state and local regulations, hospitals can help improve management oversight and lower costs by considering the following:
- Define the problem: Understand the 3 major categories of waste: Hospital, Medical, and Infectious waste and what treatments are required for each
- Segregation as a first strategy: Segregating waste at the point of generation prior to disposal is an important step to ensure health worker safety and can further assure a clean solid waste stream which can easily and safely be managed. It’s estimated that less than 10% of all hospital waste streams are infectious, requiring specialized costly treatment.
- Provide a Sharps management system: Of the 10% portion of the waste stream that is potentially infectious eliminating the indiscriminate disposal of needles helps protect hospital personal
However essential they are to facility operations, they are often overlooked in terms of their importance, costs, and improvement opportunities. By communicating with the client and showing examples of how attention to these details can benefit the efficiency of the whole facility, we can ensure that the design supports material management, rather than fights it. Looking towards the future, there are exciting design opportunities that will come with implementing strategies for automated guided vehicles, which can support improved materials management within healthcare facilities.
HMC’s Role in Healthcare Facility Layout and Material Management
At HMC Architects, we have decades of experience in the healthcare industry and are dedicated to making sure that they are designed to function at an optimal level for our clients. We’re well-versed in material management needs and are happy to work with our clients on any concerns they have about getting the most out of their projects. To learn more about how architecture and facility management go hand-in-hand, contact HMC Architects today. For specific questions related to material management and facility layouts, email Senior Healthcare Planner Christopher Naughton directly.